Meet Black Sheep Custom Builder James Bleakley
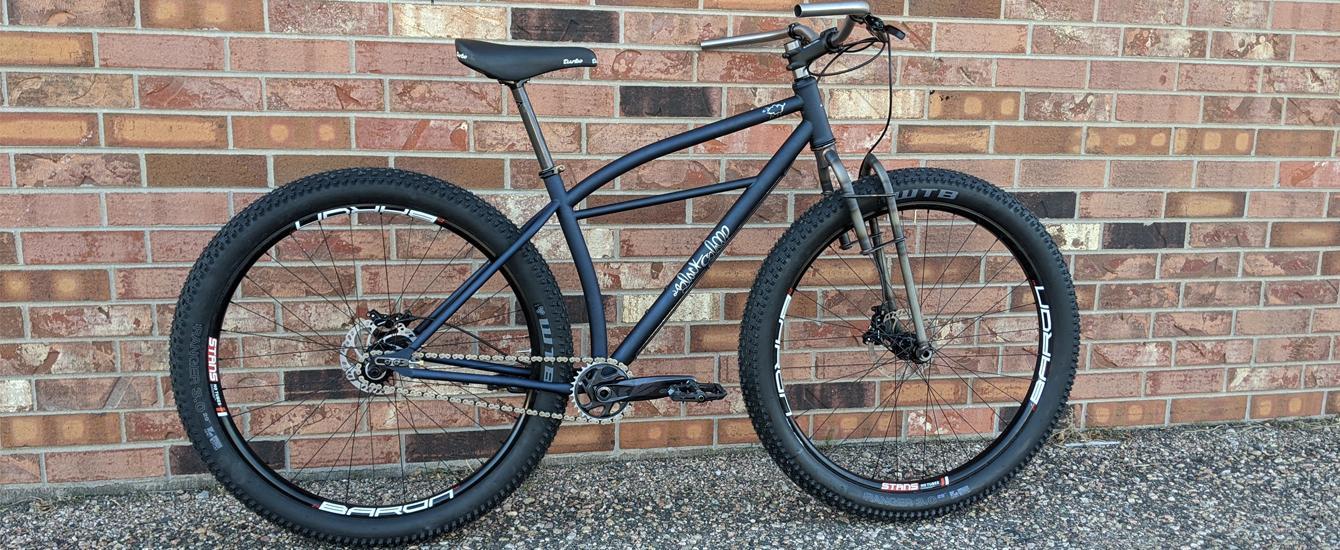
James Bleakley has been involved in building bikes for more than three decades. After learning the basics of bike assembly, machining, and welding at Boulder Bikes in the early 1990s, Bleakley further honed his welding and fabrication skills at Advanced Alloys before going on to start his very own brand: Black Sheep Bikes. Over the years, he’s also welded bikes for other manufacturers, but today he focuses on making his brand’s unique bike frames and components out of both titanium and steel. We chatted with James to learn more about what he builds and why.
Photos provided by Black Sheep Bikes
Stan’s NoTubes: Where did the name Black Sheep come from?
James Bleakley: I was wrenching for Boulder Bikes out of the back of an old Ford E150 van with a trailer at a downhill race in Big Bear in 1992 or 1993. We were parked next to other vehicles like the Ringle van and John Parker’s Yeti van, and we didn’t really fit with their rigs.
Someone said, “Wow, we really are the black sheep here.” I thought at the time that “black sheep” could be a good brand name, and I kept it to myself for a while, then used it when I started the brand in 1999. Black Sheep is about craftsmanship that stands out in a crowd.
SNT: You’ve built a lot of different things over the years. What kinds of frames and components are you making these days?
JB: The material we primarily work with is titanium, and we make a number of models of custom frames, forks, handlebars, seatpost, and stems from it. All are built-to-order.
We also have a line of steel bikes that we call our Klunker series. We have a classic Klunker -- think single gear, bolt on a coaster brake, and go -- and a modern Klunker, which takes disc brakes, thru axles, and gears. They come in four sizes.

SNT: How many frames vs components do you build?
JB: Well most of the components we make go out the door on complete bikes. If we build 60 frames per year, 30 are complete bikes, and we’ll make 40 custom forks in a year. We’ll make 50-60 titanium seatposts and 100 bars that are mostly titanium and some steel.
SNT: Ok, let’s start with titanium... why do you like to build with titanium?
JB: The thing I like most about titanium is the fact that it’s one of the lightest and strongest metals. I first started welding with it 30 years ago. Back then, there were limited tube diameters and wall thicknesses. Now there is a plethora of diameters and wall thicknesses, and you have so many options to optimize the build.
Titanium is a material that’s 60% of the weight of steel for the same volume whereas aluminum is 30% of the weight of steel. Yes, aluminium is lighter, but you have to take into account the tensile strength of the materials. Titanium is stronger compared to aluminum and resists fatigue better. Aluminum doesn’t endure as well as titanium and steel.
I love the versatility of the titanium as a material, especially its non-corrosive characteristic because only one in 10 of the bikes we build stays in Colorado. I don’t have to think about the climate where our bikes are going.
Another advantage to titanium is that it has 20% elongation. That translates into us being able to put some vibration damping in our builds without the added weight and complexity of suspension.
SNT: So what about steel?
JB: I started with steel. I was using super steel sets from True Temper, Columbus, Reynolds, Dedacciai, etc. They were about twice the tensile strength of regular chromoly steel. When you welded those bikes, they got stronger in the weld zone rather than annealing. That shifted the mechanicals toward making stronger and lighter bikes.
I still enjoy riding a good steel bike. It has a lively feel, but is predictable under hard pedaling. You can preload into corners. It also has a natural damping characteristic - not as much as titanium but still good.
I stopped building steel bikes in 2008, but then I went back to them for my Roots line. I wanted to create something that was cheaper for the consumer and also easier to produce. Hence the stock sizes and lines, which prevents CAD drawings from having to get passed back and forth with the client.

SNT: What are your favorite things to build and why?
JB: I really like our titanium fork. That’s one of my favorite forks. It has the capacity to change the ride for a rider. A lot of forks we make are meant to take the place of or mimic short-travel suspension through regular vibration damping by using the properties of the titanium. I make a unicorn fork, and I make a four-leaf titanium fork that’s a pseudo-suspension. That design tends to brace the fork vs. making it more mobile.
I’ve also come up with a plate/crown fork (aka the Burro adventure fork) for gravel bikes. It achieves a short fork axle to crown length but still fits larger tires, and it works on contemporary bikes and retrofits on older bikes, so I can adapt the fork to different bikes and riders with minimal changes to the design on my end.


SNT: You create a lot of unique stuff. What are the challenges and rewards of blazing your own path and making truly unique bikes and components?
JB: The challenge for me is often different from bike to bike. I’ve always said that form follows function, which means I want good aesthetics but not at the expense of performance. I want to make something that’s aesthetically interesting and still works. I won an award at the North American Handmade Bike Show (NAHBS) in 2008. I spent a lot of time after that trying to figure out what to make next.
As drivetrains and other components evolve, it changes the way you can design bikes. 1X drivetrains and thru axles are the two big ones. I’ve had to embrace those changes and adjust in building new stuff. Having been in business building Black Sheep since 1999, a number of the bikes I’ve built feel outdated. So trying to build on previous designs but modernize them is a challenge I love. For example, I’m on the fifth or sixth iteration of a titanium softail suspension bike. The design continues to evolve. It gets stiffer and lighter. Some of that is due to tube shape, thickness, and diameter, but some is due to the components evolving. It’s fun to work with the newest stuff on the market to recreate some designs I’ve built for the last 15-20 years but do them in a way that feels contemporary like having more lax head angles, internal cable routing, dropper posts, and wireless shifting.
Somebody once referred to Black Sheep as “expensive weird shit.” At first, I was offended, but now I can see why they would say that. Someone also once said that if you took all branding off things and put them in a pile, they could pick mine out of a pile. We’ll never be a big company because I want to put my hands on everything that goes out the door. I prefer small and handcrafted. Over the years, we’ve been pigeonholed as the guys that make curvy weird stuff, so I don’t even really have to sell what we do. Black Sheep sells itself now.
SNT: Have you ever had any custom build requests that ended up being impossible?
JB: Oh yeah, absolutely! People want bikes with just chainstays and no seat stays. Sometimes what’s in a request is impossible, and I have several of those on my desk right now. Tire clearance requests are one example. It’s just not possible to have a chainstay length that gives as much tire clearance as some people want. People want a bike that can do everything, so I have a lot of conversations about what can coexist at the same time.
I get cocktail napkin sketches of things that are so curvy that I can’t bend them that way. It’s just not possible. Or I’ll just know that it wouldn’t ride right when it’s built and loaded. When I get impossible requests, I usually end up in a conversation about how to make something functional yet maintain the elements of the design that they are drawn to. Sometimes the design does end up in the wastebasket, but often we can adjust it and find something that will work.
An example of something that came out of this process is a telescoping chainstay (vs. a sliding dropout) as a tensionsing system for a singlespeed. It also turns out to be a good way to pack a bike in a travel case.

SNT: It’s always interesting to see what builders are riding. What are your current personal bikes?
JB: I like that you said “bikes” not “bike”!
For years, though, I just rode one bike - it was always my single speed fat bike with a 46” gear ratio. It’s still my favorite bike and my go-to bike. It’s my default race bike for big events like Leadville.
I’m also riding a steel Klunker with our Deathsplosion fork with coaster brake only. It’s got a 2:1 gear, so I use it mostly for townie and gravel use. I’m reluctant to take it on trails.
Third is my steel gravel bike with our titanium Burrow adventure fork. It actually has gears. I’m using a Force 2x11 drivetrain, but I’m using it as a 1X as I have the front derailleur lever operating the dropper. It has Stan’s Grail CB7s on it which I just love!
SNT: Speaking of Stan’s wheels, why do you put them on the bikes you build and ride?
JB: I like that they are easy to seat with tires even with a hand pump. For example, I’ve run Stan’s Hugos for years on my fat bike. They are the only tubeless fat bike setup you could set up out of the box with a hand pump. I ride that fat bike everywhere all the time. And I’ve got Baron 29er hoops on my single speed titanium bike with 3” tires.
I want to be able to get a flat in the middle of the night in the winter, fix it easily, and get going again. But I’ve never had to put in a tube in five years. I just carry extra Stan’s to squirt in more sealant if I need it. Usually, what’s happened is that I’ve just forgotten to top off my Stan’s for a few months.
Stan’s wheelsets are a great bang for the bike. They are lightweight and affordable. I can spend more on wheels, but I can’t get that much more performance-wise for the extra spend. I also love that Stan’s is continuing to innovate. The Arch and Flows are in their fourth (MK4) generation.

SNT: We’ve been hearing a lot about supply chains. Has Black Sheep been affected?
JB: Yes, we’ve been affected. I used to take supply for granted out there in the market. Now I have to put more of my inventory dollars into components rather than just materials.
We currently have a seven-month lead time in titanium bikes. In the past, I was able to wait until just one month prior to delivery to order parts, but now I have to be more proactive. Sometimes I start looking for parts right away. I’ll guess what I’ll need and pre-order parts ahead of time, so I have them when I need them. Sometimes, I have to find other channels to get parts just to be able to finish out a build.
SNT: What bike design trends have you been seeing?
JB: I’m seeing changes to thru axle and hub spacing conventions, the number of gears and gear ranges. There are longer top tubes and slacker head angles. Big changes in steering geometry on mountain bikes are giving them better manners going downhill fast and allow for longer travel forks, even on a hardtail.
Shorter chainstays are another thing. We used to have 16.75” chainstays on 26” mountain bikes, but even our 29ers have shorter chainstays now. We make those happen by using yokes to keep it thin where tires and chains are. A curved seat tube also lets us shorten the chainstay.
Finally dropper posts have been another big change. They let you move your weight back and down, changing where your center of gravity is. The wheels are coming more and more underneath you.

SNT: Is there anything you’d like to see happen bike innovation-wise in the future?
JB: I’m always looking for better fat bike rims! I know that fat bikes are largely dead or relegated to the lower end of the market, so it’s not likely to happen, but my fat bike is my favorite bike to ride. It’s 26 pounds and titanium, so it’s a sleeper. It looks massive, but it's a featherweight even with 5” tires.
I’d like to see bigger volume, lighter tires whether it’s a 29er wheel with 4.0” tires or more options in the 26er such as a 4.8”. Tire innovation would be great, especially if the sidewalls were more protective. That said, yes, tires are already going the way of getting bigger. Personally, I don’t mind a bigger tire and more rolling resistance as long as I have a big smile on my face, and I can go ride anywhere including getting off the roads.
SNT: Any parting thoughts?
JB: What’s important to me as a builder is that I have a chance to connect with the next generation of people coming up in the industry and share what was passed down to me. I feel like I have an obligation to pay forward so I teach one week of the year in the bike building program in Iowa, and I mentor kids in the local community. I bring in aspiring frame builders to teach them what I do know.
Some people want to hold their knowledge tight, but for myself, I want to share what I’ve learned so people can pick it up and expand on it. Everyone else benefits from that, and I don’t want frame building to become a thing of the past in this country.